Weaving Mill
In our weaving mill, we give air the right direction.
Drafts, uneven airflow, performance losses. The problem isn’t the system—it’s the material. Most manufacturers buy their fabrics. We don’t. We weave them ourselves.
HISTORY
A story that began on an old Danish farm
Airflow Begins at the Fiber
Not every textile can withstand years of continuous operation while maintaining its original properties.
Every meter of fabric is produced on cutting-edge weaving machines, where we control multiple factors to ensure consistent quality.
In 2019, we introduced Albot, a robot that took over the most demanding part of the process—preparing the yarn for weaving. Automation allows us to achieve higher efficiency, consistent quality, and reduced physical strain, all while maintaining our commitment to craftsmanship and precision.
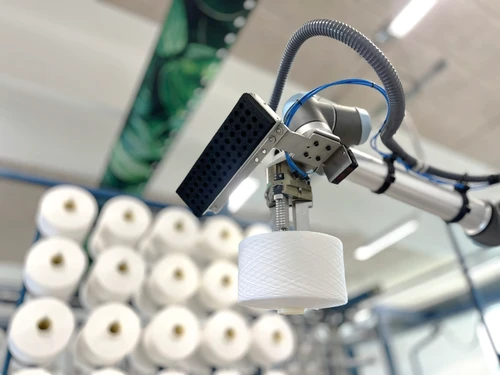
What Materials Do We Produce?
Same yarn, different processing—two fabrics to meet all your needs.
For these textiles, we use flame-retardant polyester fibers, sourced from the same granulate for both materials. However, due to different yarn processing techniques, each fabric gains its unique properties.
- DFC-HT is made from longer, parallel-aligned fibers, giving it exceptional strength and durability.
- TCS, on the other hand, is made from shorter fibers that slightly protrude, enhancing its dust-catching capability.
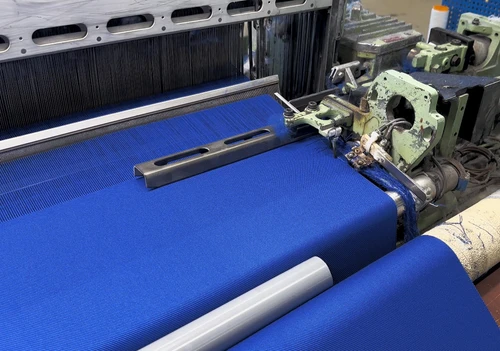
Smart Dyeing: More Colors, Less Water
Traditional dyeing methods consume up to 25 liters of water per kilogram of textile.
We have moved away from this approach, adopting more efficient and eco-friendly technologies that significantly reduce water consumption while ensuring maximum colorfastness.
- Cone Dyeing – Dye is applied directly to the yarn on the cone, allowing it to penetrate the fibers gradually. Water consumption: only 5 L/kg.
- Dope Dyeing – Pigment is added during the granulate production stage, resulting in zero water consumption.
- Transfer Printing – The color is transferred directly onto the fabric using a printing press. This method allows for over 1,600 colors, patterns, and prints with minimal water usage.
This approach has led to a 67% water savings compared to traditional methods, while guaranteeing high colorfastness and uniform shades.
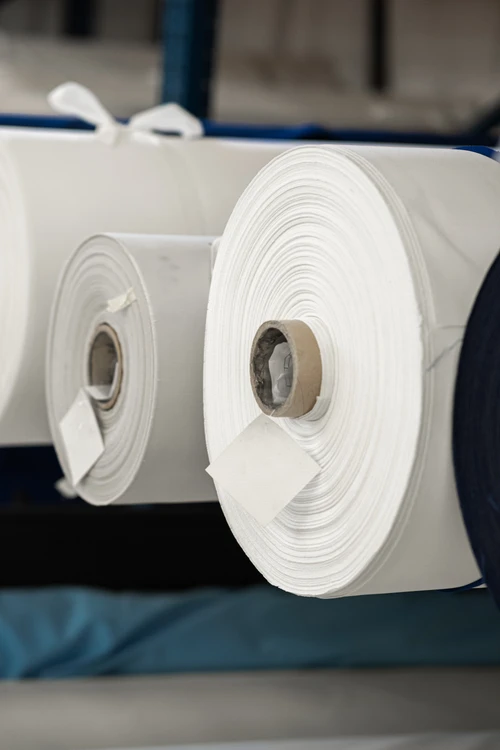
Permeability: The Key to Even Air Distribution
Even airflow doesn’t happen by chance—every material detail influences how air moves.
- This unique property is achieved through a special warp preparation process, where constant yarn tension is maintained during winding.
- During weaving, we adjust the weft density to achieve the precise permeability required.
- Finally, the fabric is thermally stabilized to ensure it retains its properties even after repeated washing. Thanks to this fixation process, we offer the best shrinkage guarantee on the market—only up to 0.5%.
Every 600 m² of fabric is inspected to ensure that the weaving meets strict airflow performance parameters.
SEE HOW IT WORKS →
Committed to the Environment
Having our own weaving mill allows us to manage the entire process sustainably—from raw materials to the finished product.
- Residual yarn is recycled and repurposed into hanging cords for installation.
- Plastic spools are crushed and reused to produce corner elements for FBS panels.
- Textile offcuts don’t become waste—they are repurposed, for example, in acoustic panels.
- Water savings in dyeing – thanks to innovative methods, we reduce water consumption by up to 65%.
Our goal is zero final waste because we see an opportunity in every single product for further development and innovation.
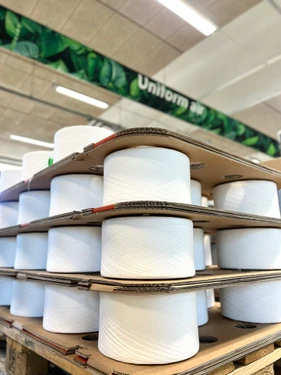
Get in touch with us
The refreshing air you desire is just 1 click away.Our expert sales representatives are ready to advise you on design or handle any project.
With us, you can expect a response to your request within 24 hours.